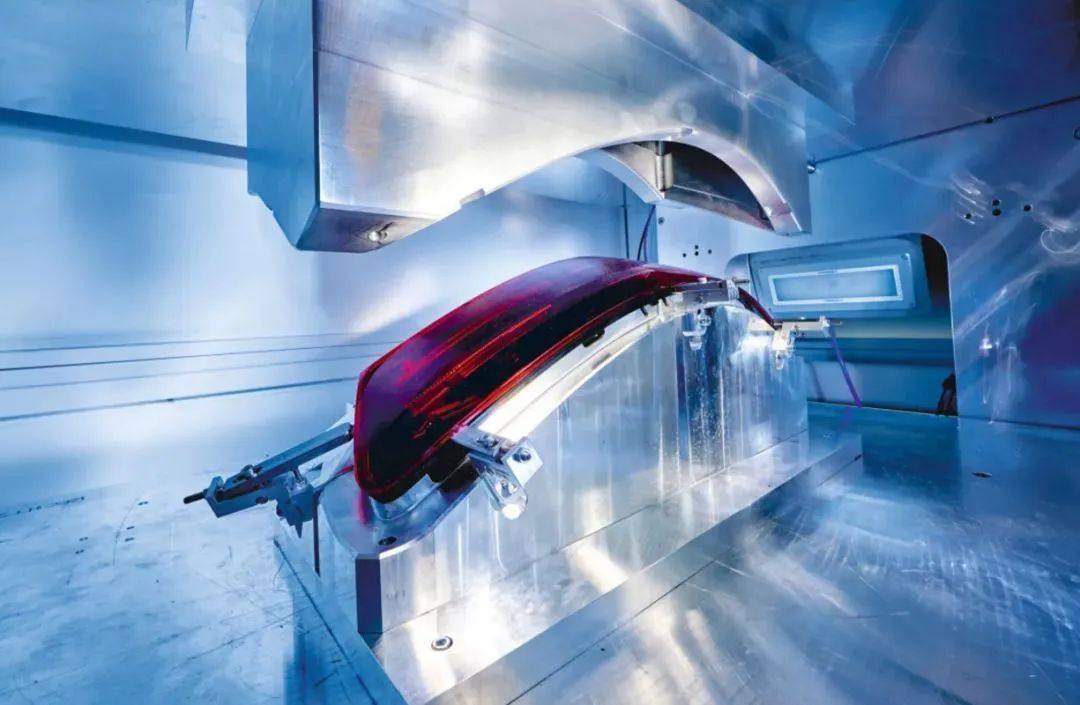
长久时间以来,塑料的连接都是一个难以实现满意解决的难题。
一件塑料制品也许会由多种部件制成,要将各部件接合起来,可运用化学粘接、机械紧固及热效应焊接三种方法来处理。在这三种接合办法中,传统的化学胶水粘接能获得优良的性能和优质接头,但是操作困难,需要精心地进行接头和表面制备,速度很慢,不适合大批量生产,且常常散发出异味,甚至产生甲醛等有毒物质,不符合环保要求;机械紧固连接速度快,可快速将两种部件衔接,但接缝的防漏作用较差,局部应力也会变大,从而导致聚合物材料之间脱离;而利用热量熔化塑料进行拼接的焊接方法是永久性连接塑料部件的最有效方法,其力学功能接近于母体材料,且焊接形式多样,可依据不一样的材料、尺寸和用途而采用不一样的焊接方法。本文重点探讨的是塑料的焊接。
塑料焊接步骤
通常来讲,热塑性塑料的焊接分为五个步骤来展开:
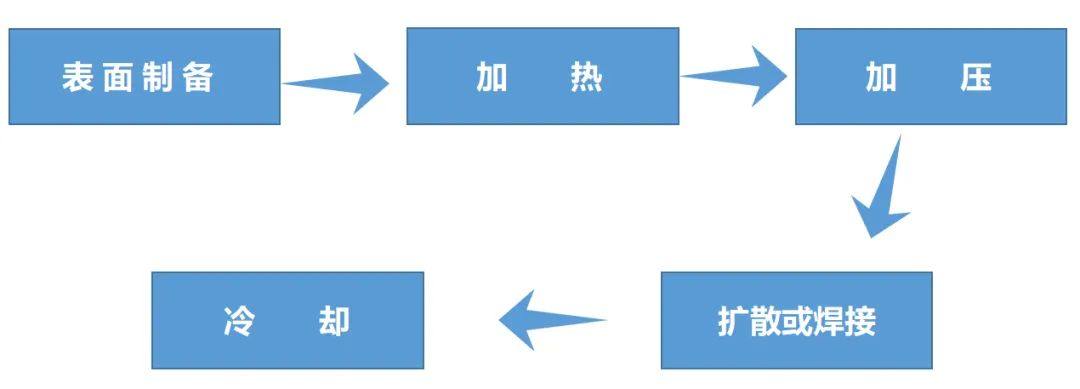
1
表面制备非常重要,因为大部分模压成形的塑料制品其表面均有一层脱模剂或污物,必须清理干净,才能使焊接顺利进行。
2
加热有多种方法,也是区分不同焊接方法的主要依据。
3
加压的方式有:手工加压、压力机加压、自动夹具加压等。
4
液体与液体界面一经建立,扩散就立即进行。对于结晶或半结晶材料扩散几乎是瞬时完成的;对于非结晶材料,如果加热温度稍高于熔点,则扩散时间会很长。
5
最后一步是焊件冷却和接头凝固。在塑料焊接接头没有达到足够支撑整个焊件的强度和刚度之前,必须一直维持焊接压力。
影响焊接的因素
在进行焊接时,压力、时间、吸热量(熔融量)是确保焊接质量的三大工艺因素。
压力——对焊接表面施加适当的压力,焊接材料将由弹性向塑性过渡,还可以促进分子相互扩散,并挤走焊缝中的残余空气,从而增加焊接面密封性能。
时间——要有适当的热熔时间和足够的冷却时间。当热功率一定时,时间不够会出现虚焊,时间过长会造成焊件变形,熔渣溢出,有时还会在非焊接部位出现热斑(变色)。必须保证焊接面吸收足够的热量达到充分熔融的状态,才能保证分子间充分扩散熔合,同时必须保证足够的冷却时间使焊缝达到足够的强度。
熔融量——热熔时间和热功率协调调整才会得到最恰当的熔融量,保证足够的分子间融合,消除虚焊的现象。
除了焊接设备和操作人员技能水平外,来自于塑料内部或外部的各种因素对焊接质量有一定的影响,如塑料的吸湿性、塑料中的填充物、焊接面的清洁等,都应当引起重视。
在选取正确的焊接材料和排除了影响焊接效果的不利因素之后,还要根据材料种类的制品形状、成本的高低采取适当的焊接方法。
焊接方法分类及特点
对于塑料的焊接,有着多种工艺方法可供选择,按照加热的方式不同,它包括有感应焊接、热板熔接、热风焊接、振动摩擦焊、超声波焊接与激光焊接等。
热板焊接
热板焊接时,一般是平面电热板将需焊接的两平面熔融软化后迅速移去电热板,合并两平面并加力至冷却,一般使用热封机进行操作。它可能是最简单的塑料焊接技术,焊接强度高,设备简单成本低。缺点是仅限于简单工件,基材易过度熔融,易“拉丝”,精度不够,自动化程度低,效率很低。主要用于汽车、家用电器和一些塑料包装等领域,应用程度不及振动摩擦焊接与超声波焊接高。
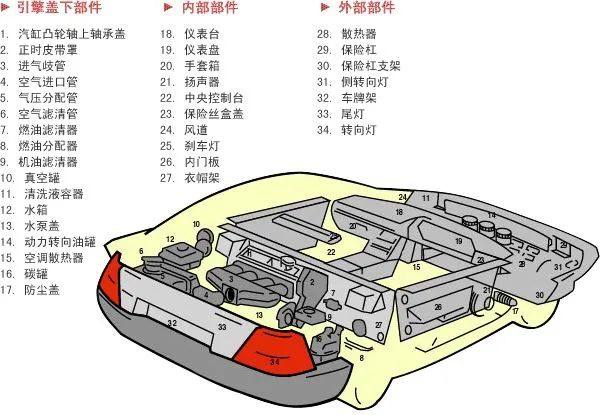
热风(气)焊接
热风(气)焊接是利用焊枪喷出的热空气或氮气对塑料焊件和塑料焊条进行加热,使焊条填充到连接部位后加热连接表面,冷却后形成接头。在各种塑料焊接方法中,热风焊历史最长,应用最广,江湖人称“万能焊”。主要优点是设备轻巧易携带,成本低,能用于连接各种大型复杂制品等。但其焊接速度比较慢,操作周期长,不适应批量加工,焊接质量受到多种因素制约,难于控制,对操作者的焊接技能要求比较高。
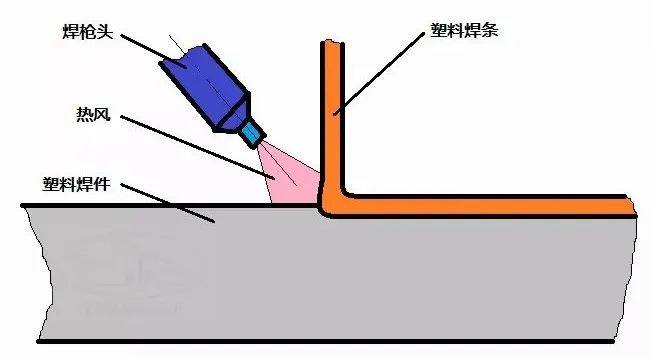
振动摩擦焊接
振动摩擦焊接是工件在接触材料表面进行高频的振动,通过摩擦达到它的熔点,然后融合。其优点是支持多工件焊接,支持大型工件焊接,焊接周期短,设备维护成本低。缺点是作为接触式方式,易产生碎屑和缺陷,而且时间长了会产生疲劳,零件就容易脱落,较大的机械应力严重影响气密性,仅限于平面轮廓焊接,焊缝较宽。
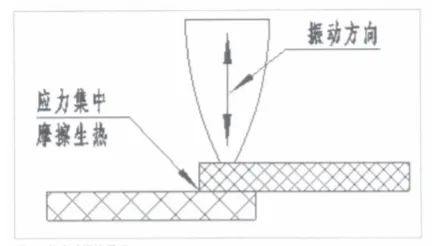
超声波焊接
超声波焊接是超声波通过被连接件,使接触表面被激发而做快速振动,发生相互摩擦,产生的热量将工件表面熔化,实现连接。优点为焊接均匀牢靠,变形小,焊缝美观,支持非平面焊接,焊接周期短(不足 1 秒),设备维护成本低,且容易实现自动化,效益高。缺点是超声波会产生噪音,易产生碎屑,机械应力大,工件尺寸及形状受限,且接口容易受热不均匀,焊接效果有误差。目前在电子、电器、汽车零件、塑料玩具、文具用品、日用品、工艺品、化妆品等各个行业广泛应用。
激光焊接
激光焊接的原理是指将透光与吸光两种热塑性工件用夹具夹在一起,透光材料在上,吸光材料在下,施加一定压力。激光束穿透上部透光工件,传输能量损失很小,到达下部的吸光材料表面,因光透不过去,光能转变成热能,使其表面熔化,同时热量也以传导方式,从底面传递到与其压接的透光工件的接触面上,使其塑化,从而实现激光热熔焊接。
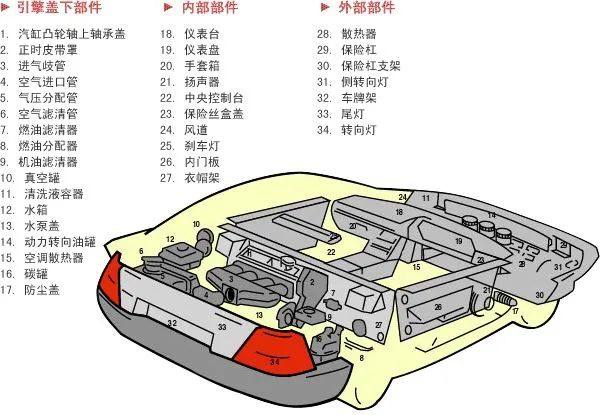
激光焊接通常用于PMMA、PC、ABS、LDPE、HDPE、PVC、PA6、PA66、PS等透光性好的材料,在热作用区添加碳黑等吸收剂增强吸热效果。与传统的超声波焊接方式相比,激光焊接具有如下明显优势:
◆洁净。非接触式处理,热塑性塑料不发生化学反应,树脂降解少。用激光焊接的塑料零部件内部洁净无碎屑,彻底解决了超声波焊接碎屑堵塞的问题。同时也适用于需要卫生安全的医疗和食品行业。
◆焊接质量好。精密、牢固、不透气、不漏水,解决了塑料制备的精密电子元器件因为超声波焊接造成的损坏器件和可靠性降低的问题。
◆焊接应力低,焊缝强度高。后期不易开裂,零部件的使用寿命大大延长。
◆外形适应性广。激光束形状尺寸可调控,从而控制热影响区和接合区域大小,自由度高,灵活性好。擅长焊接具有复杂外形的制品,能够实现二维甚至三维的焊接,为多样化定制化零部件的生产提供了基础。
◆外观出众。采用穿透焊的塑料激光焊接,外表面洁净光滑,无焊接痕迹,能够达到强度和外观两全其美。
塑料激光焊接技术最早出现在上世纪 70 年代,但因为存在一些问题,导致无法同更早出现的振动焊接、热板焊接相竞争。问题一是初期设备投入成本相比传统工艺更高;二是对基材光学性能有要求,不同颜色塑料之间搭配对激光吸收造成的焊接难度更大;其三是目前对塑料激光焊接的各种应用场景、上下料、夹具、自动化等研究仍然不足。
从 90 年代中期开始,由于激光焊接的设备费用下降,该技术才渐渐受到人们的欢迎。特别是近几年,由于环保被越来越重视,工艺成本大幅下降,加上激光焊接专用塑料开始国产化,所以塑料激光焊接技术逐渐崭露头角,被提及的频率增多,在汽车、医疗器械、包装等领域得到了比较广泛的应用。本文接下来聚焦于激光焊接在汽车行业的应用。
塑料激光焊接技术推动汽车产业升级
在各种热效应焊接方法中,激光焊接被广泛地应用于汽车制造行业的塑料焊接领域,包括自动门锁、无钥匙进出设备、启动开关、胎压监测计、仪表盘外壳、电子驻车制动系统(EPB)、前灯和尾灯、进气歧管、燃油喷嘴、燃油泵、变档机架、发动机传感器、驾驶室机架、液压油箱、变速箱过滤器、气液分离器、新能源汽车电池等塑料零部件中,并发挥了良好效果。国外新车型中的塑料零部件采用激光焊接的比例已经高达95%以上,而超声波焊接则面临着被全面替换与淘汰的窘境,因此汽车零部件行业中越早开始使用激光焊接的企业将抢占到产业升级的先机。
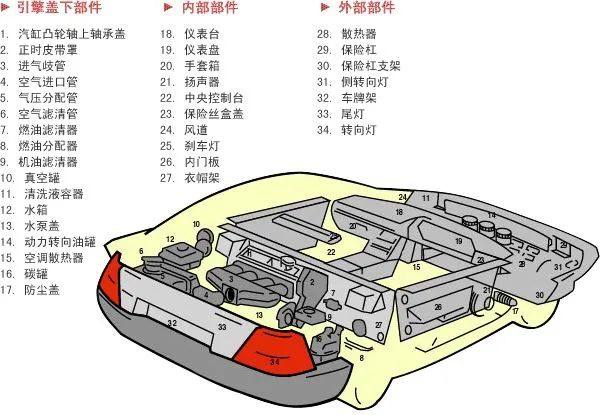
以汽车尾灯为例,它是车身外少有暴露的塑料零件之一,现如今的贯穿式尾灯集转向、刹车、倒车照明、示廓、雾灯等功能于一体,且被设计得越来越大,长度通常可达1400毫米,其复杂的3D设计极具美观度和辨识度,成为众多车企吸引消费者眼球的利器之一。制造商需要在尾灯薄件上实现严格的公差,达到无碎屑焊接,同时保护精密组件和内部的电子设备。尾灯的焊接工艺一直备受瞩目,甚至坊间有种说法:焊得好不好,决定了尾灯的成品率、美观度及密封性。
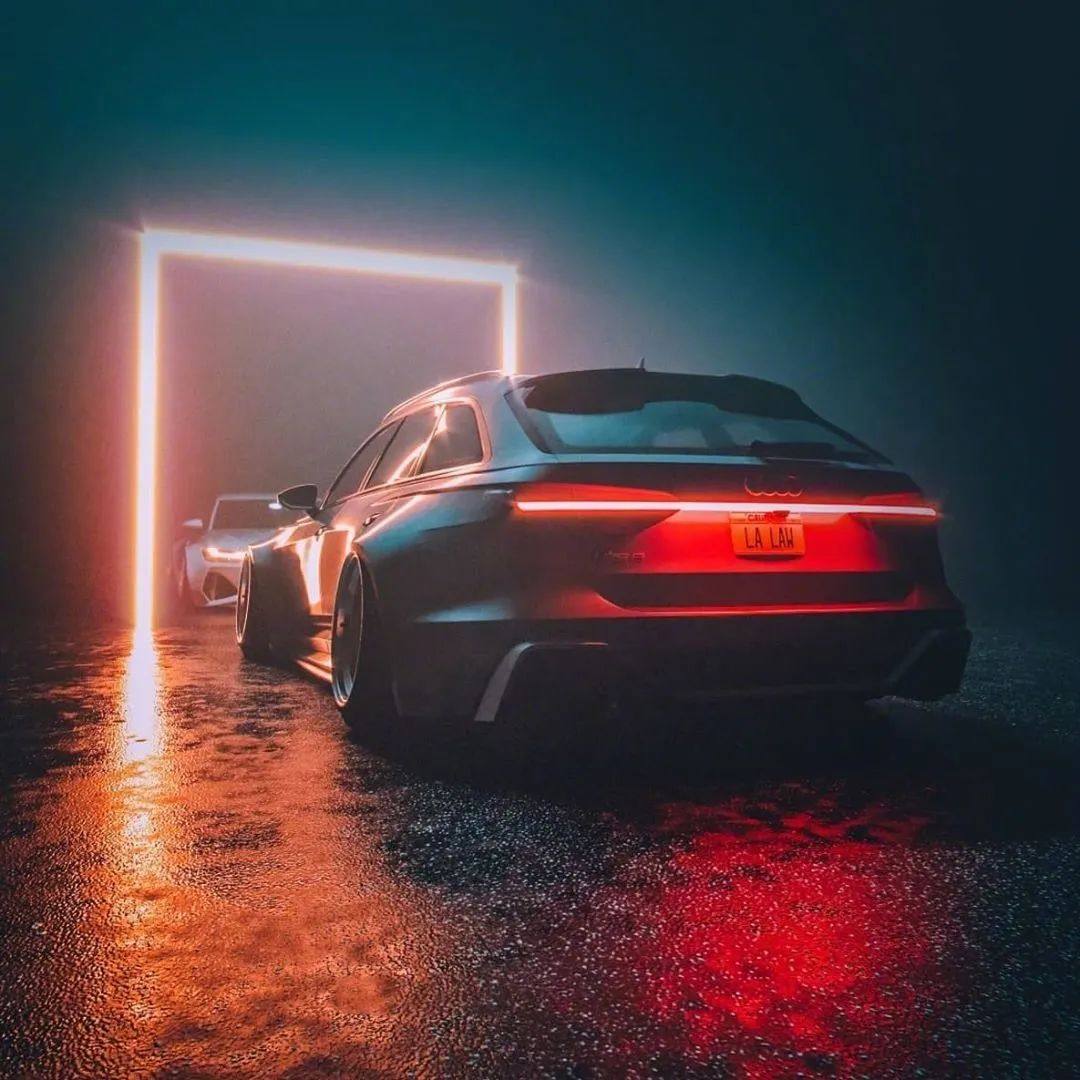
如前所述,市场上最为主流的尾灯焊接工艺主要有振动摩擦焊接、热板焊接、超声波焊接、激光焊接这几种。震动摩擦焊接和热板焊接占据了尾灯焊接市场份额的半壁江山,它们具有焊接技术高度成熟及设备成本较低的特性,但是这两种工艺也有其技术壁垒,主要归纳为:尾灯外观结构受焊接规则限制;焊接过程不清洁;焊缝不美观;焊接后机械应力较大等缺陷。可以取代它们的,当然就是高大上的激光焊接!
目前尾灯激光焊接领域主要有两种主流工艺:其一,激光同步焊接方式,来自多个二极管的激光束被引导到沿着焊接层的轮廓线上,并熔化塑料,从而使得整个轮廓同时熔化并粘结在一起,呈现出焊接轨迹的光斑,特点是内应力被减小了;其二,基于3D机械手的激光混合焊接方式,多色光源(如卤素发生器)用作辅助热源,这种组合提高了加工速度,加工出可靠、美观、几乎无应力的的高质量焊缝,无需后续处理。以上两种焊接工艺都已经在尾灯焊接领域取得了不俗的业绩及市场占有率。但它们并非完美解决方案,因为激光同步焊接的要求比较高,整个价格也比较高,动辄上千万一台的设备,让大部分的车企望而却步;而激光混合焊接的工艺过程较难控制。
那究竟有没有一款设备可以在成本经济的前提下做到工艺成熟呢?LPKF(乐普科)公司推出的摆振焊接(Wobble Welding)技术给出了答案。这是针对大型三维部件的特殊焊接工艺,激光束垂直于送料方向偏转,有着更宽的摆幅,因此可以轻松地在1mm到5mm之间调节焊缝宽度,且温度分布特别均匀,局部公差可抵消。它革命性地将激光尾灯焊接设备的成本压缩到不到同步焊接设备的一半,全新设计的上下结构治具,有效地克服了传统混合焊接工艺复杂的困扰,且治具成本只有之前的五分之一。LPKF的PowerWeld 3D 8000设备通过一套更先进的软件进行控制,大大提高了设备的灵活性,并使该设备可以轻松地与客户自己的MES系统进行连 接,配套WeldPro®系统程序及用于项目快速设置的3D软件。这两个程序都能自动控制摆振功能,即使当焊接件高度发生变化时也能确保能量输出的一致性。因此,这款巨无霸最大可以焊接尺寸为1000mm*750mm*400mm的超大型尾灯或同等大小的零件,不论是短小精悍的转向灯,还是超大超长的贯穿式尾灯,对于PowerWeld 3D 8000来说都能轻松驾驭。
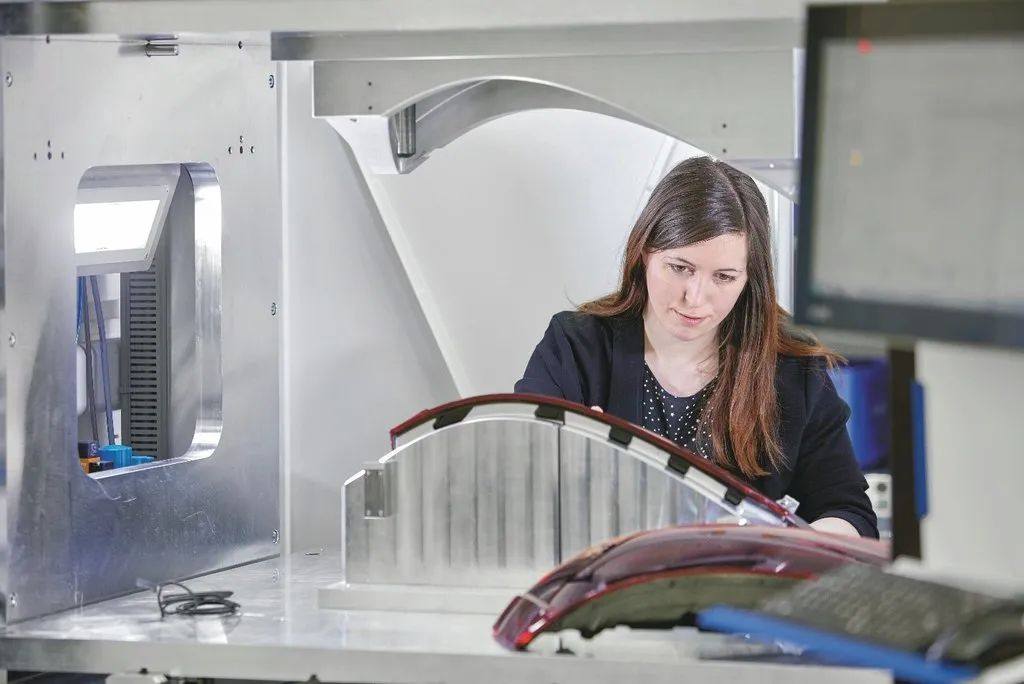
除了尾灯,激光焊接技术还被应用在高档轿车的保险杠上,其优点是输入的热量较低、外观好,并可获得很高的焊接强度。保险杠材料大都采用PP、EPDM(三元乙丙橡胶)和10%的滑石粉共混物,以及PC、PBT等。以前采用超声波焊接将停车距离传感器的适配器焊接到已经上好漆的保险杠上,然而在强度和外观之间难以达到两全齐美。采用激光透射焊接工艺焊接保险杠的传感器适配器,产生的熔化物很少,因此没有熔化物溢出,在具有良好强度的同时,外观优美。不过激光焊接的投资费用目前还较高,只有在要求较高时使用才经济。保险杠的结构设计的未来趋势是材料的壁厚越来越薄,这特别适于采用激 光技术。除了对材料和加工的新要求之外,采用激光工艺使焊缝的形状和位置有了更大的自由度。由于单位焊接强度一般高达60MPa,并且安装空间将更狭窄,因此为激光焊接的应用创造了很好的机会。
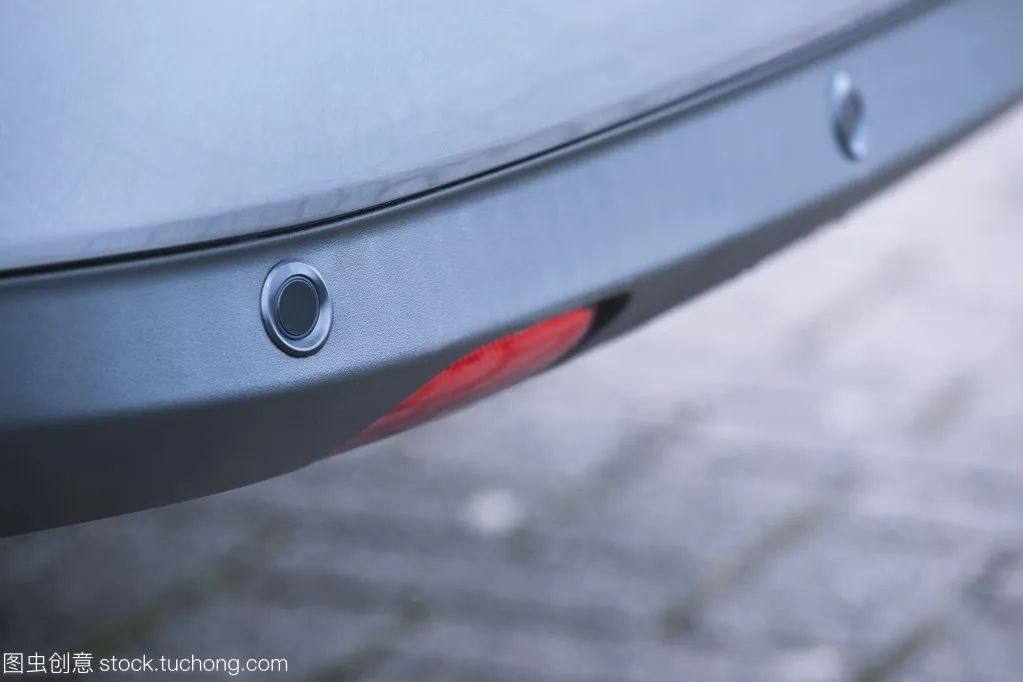
Conclusion
作为热塑性塑料二次加工的主要方法之一,塑料焊接已成为汽车等产业生产技术水平及新材料开发水平的标志之一。随着工业生产的需要,塑料焊接技术会得到更加长足的进步和更加广泛的应用,也一定会有技术更为先进、使用更为方便的焊接新方法出现。
原创文章,非授权严禁转载
-作者:马维博(图片源于网络,侵删)
-排版:Erica
contact us
好文章就是要分享!欢迎大家踊跃投稿~
投稿邮箱:
lilyban@ringiertrade.com
ericazhan@ringiertrade.com
扫码索取杂志
微信号|RingierPlastics
资讯|技术 | 访谈 | 杂志 | 研讨会
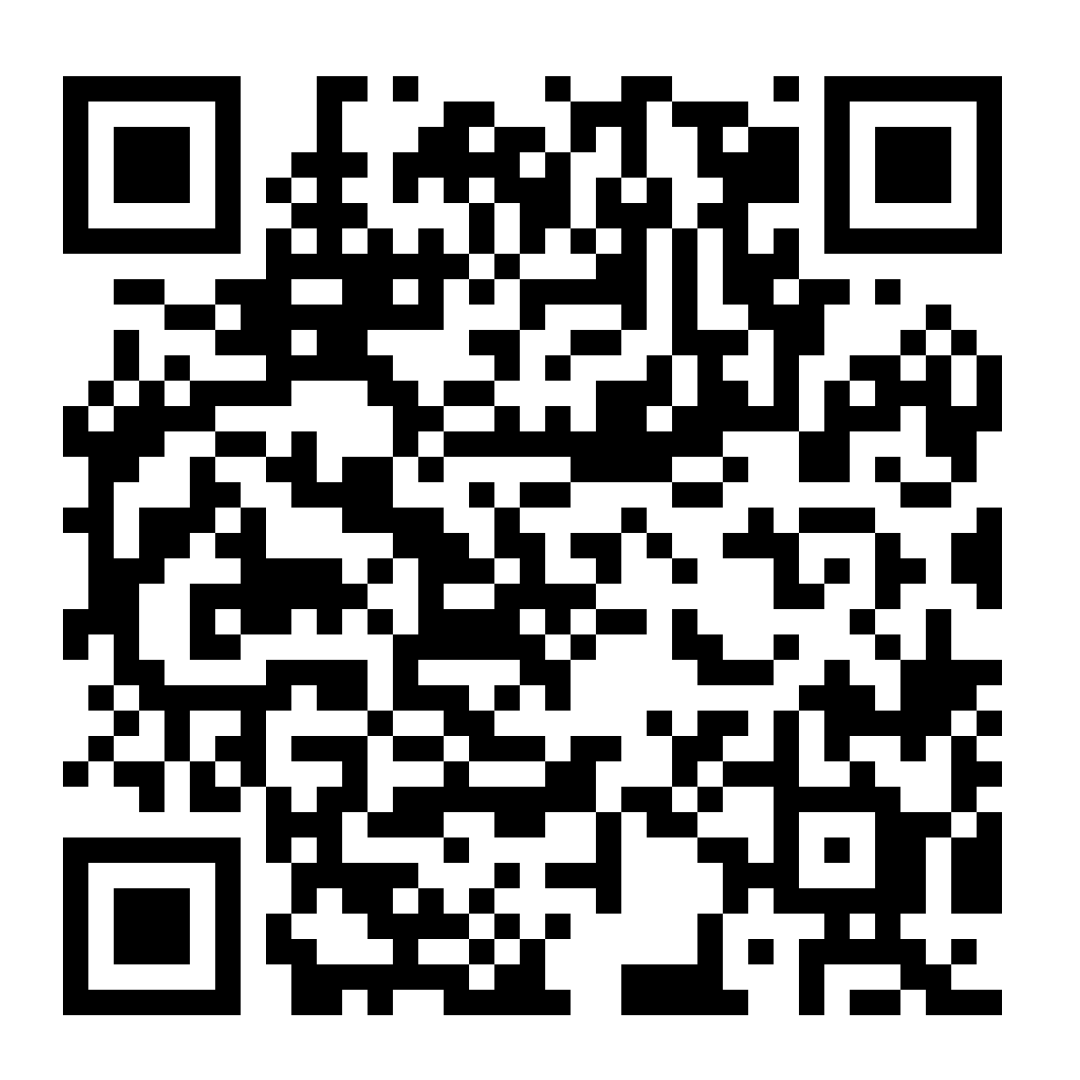
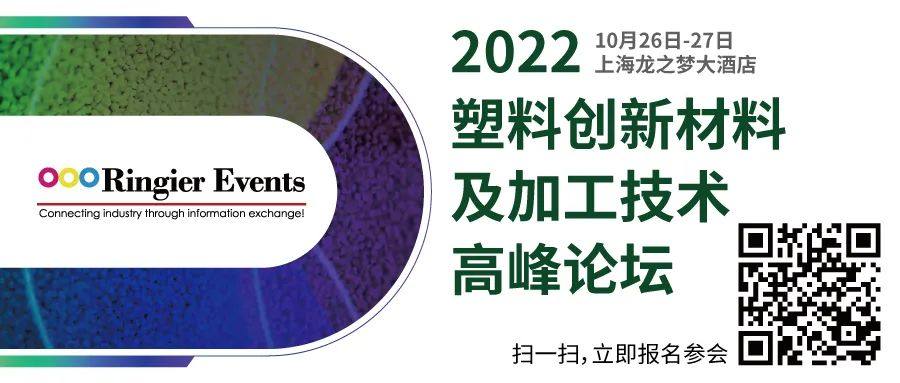
原文始发于微信公众号(荣格塑料工业):汽车尾灯激光焊接工艺如何化繁为简?