德中新3D-MID工艺:Lpum介绍
摘 要:本文主要介绍了德中一种新的3D-MID工艺-Lpum工艺的流程、原理及技术特点等。
关键词:3D-MID新工艺;塑料表面选择性金属化;激光应用;
德中(天津)技术发展有限公司 王恒亮 电话:022-83726901 手机:13821999591
一、3D-MID概述
3D-MID一般指Three Dimensional-Molded Interconnect Device(三维模塑互连器件);或Three Dimensional-Mechatronic Integrated Device(三维机电集成器件)。
3D-MID技术能在注塑成型的塑料壳体的表面上,制作有电气功能的导线、图形,并直接在壳体上安装元器件并使其电气互连,从而实现电路板的电气互连功能、支承元器件功能和塑料壳体的支撑、防护功能以及由机械实体与导电图形成结合而产生的屏蔽、天线等功能集成于一体,形成"三维模塑互连(机电集成)器件"。
常用的3D-MID技术有以下几种:
-
德国LPKF公司的Laser Direct Structuring(激光直接成型)工艺,步骤为:注塑成型—激光活化—化学镀铜+化学镍金。
-
日本Sankyo Kasei公司Two Shot Molding(两步注塑)工艺步骤为:非电路部分注塑—电路部分注塑—化学镀铜+化学镍金。
-
日本松下的Laser Resist Imaging(激光选择性去抗蚀剂)工艺,步骤为:工件注塑—化学镀铜—涂覆抗蚀剂—激光选择性去除抗蚀剂—蚀刻—表面处理(镍、金等)。
-
美国OPTOMEC公司的AJ/Aerosol Jet(气溶胶态直接喷印)工艺,步骤为:工件注塑成型—喷印气溶涂料—用氙灯或激光或烘炉烧结。
-
奥地利公司Plasma Innovations(等离子涂覆)工艺。该工艺用低温+微细+常压下的等离子涂覆导电材料方法,直写导电结构,阳极和阴极间的电弧产生等离子流,其能量将输入的铜颗粒熔化,喷到基材上,直接形成导电结构。
其他工艺还包括pcb图形镀的3D-Photoimaging工艺、Hot Embossing技术及经激光修整的LRP技术等。
根据各工艺的机理简单归类总结如下:
图1 3D-MID各工艺机理归类总结
各工艺的技术参数及优缺点:
工艺 |
最小线宽/间距 |
加工速度 |
高温 |
优点 |
缺点 |
Laser Direct Structuring |
150/100μm |
1~2m/s |
/ |
出色的三维布局能力 |
需要添加LDS粒子,原材料成本高 |
Two Shot Molding |
200/200μm |
/ |
/ |
工艺成熟、适合大批量生产 |
开发成本高、工艺复杂 |
Laser Resist Imaging |
75/75μm |
/ |
/ |
与PCB工艺接近,工艺成熟 |
三维布局能力差、工艺复杂 |
Aerosol Jet |
100/50μm |
10~20mm/s |
200℃ |
线路精细、基材表面要求低 |
加工速度慢、导线导电率低 |
Plasma Innovations |
2/1mm |
250mm/s |
/ |
导电层可以很厚 |
线路粗糙、基材表面要求高 |
3D-Photoimaging |
75/75μm |
10~20m/s |
/ |
与PCB工艺接近,工艺成熟 |
三维布局能力差、工艺复杂 |
LRP |
100/50μm |
/ |
150℃ |
速度快,基材表面要求低 |
三维布局能力一般,导电率低 |
表1 3D-MID各工艺的技术参数及优缺点
二、德中Lpum工艺
Lpum(Laser Patterning Undoped Materials)工艺,是德中自主研发的可在塑料基材上选择性金属化的工艺,为一种全新3D-MID技术工艺。Lpum工艺采用不添加LDS粒子的普通塑料基材,通过特定的激光加工方法,可控改变材料表面状态,为后续活化和金属化创造所需的表面状态,并提高基材表面与金属线路的结合力。
与其它3D-MID工艺相比,Lpum工艺可广泛在红外、紫外纳秒或者皮秒等先进激光机器上使用,金属化线路更加精细。实验结果表明,Lpum工艺的激光加工方法可提高基材与金属线路的结合力,如基材与铜层之间的剥离力可以达到0.54—1.46kgf/cm。
图2为Lpum工艺的流程图:
-
普通塑料注塑:注塑时不需要添加LDS粒子。与表面哑光的基材相比,表面高光的基材选择性更好。
-
前处理:用药水浸泡、或涂覆薄膜、或等离子等工艺的一种或几种,在基材表面产生一层疏活化剂层,该疏活化层能够减少或阻止活化剂的吸附。不同种类的塑料,前处理工艺有可能不同。
-
激光加工:激光加工有疏活化剂层的基材表面,可破坏并去除图形部分的疏活化剂层,使得图形部分与非图形部分对活化剂有不同的吸附性能;此外,激光还可改变图形部分的表面粗糙度,提高图形部分与金属层的结合力。
-
活化:由于激光加工造成吸附性能的差别,当活化剂在基材上沉积时,图形部分会多沉积,非图形部分少沉积或不沉积,提高了选择性。再经过去除速率均匀的除活化剂步骤,反应一定的时间后,可将非图形部分的活化剂全部去除,只保留图形部分的活化剂。
图2 Lpum工艺流程图
-
金属化:金属化的第一步是化学镀。正常情况下,金属离子在有活性中心的地方才会结晶沉积,没有活性中心的地方不会沉积。但如果药液活性很高,就会出现在没有活化中心的地方也沉积,所以化学镀药水的管控非常重要,起镀速度和沉积速率高或低都会导致溢镀或者漏镀。基材表面沉积一层金属后,就可以电镀增厚、沉镍金或者电镀镍金等。
相比较其它3D-MID工艺,德中Lpum工艺有以下优势:
-
使用普通基材,在注塑时无需添加LDS粒子,降低基材成本。
-
可兼容使用紫外纳秒、紫外皮秒等先进的激光器。光斑小,线路更加精细化。
-
采用特殊激光加工方法,可控调节基材表面状态和结合力。
-
激光加工同步实现基材的粗化,无需化学粗化,工艺绿色环保,成本低。
三、Lpum工艺性能
1、精细化的线路:
Lpum工艺采用脉冲激光加工方法,通过设置足够大的加工路径间距和扫描速度,以单个激光脉冲或者脉冲串与材料表面发生反应,最终在材料表面形成一定排列的、没有叠加的微坑。
如图3所示,该图是激光以单个脉冲或者脉冲串与材料作用后,形成有序排列微坑的SEM图。为了方便观察,相邻两个微坑中心的距离设置为50μm,以平行的激光加工路径为例,线与线之间的距离即为上下行相邻微坑的中心距离,而脉冲激光的扫描速度除以频率则为左右间相邻微坑的中心距离。因此,通过调节线宽、扫描速度和频率来控制微坑的中心距,从而有效调节微坑排列的密集程度。
功率越大,微坑直径越大,当微坑中心距设置小于微坑直径,相邻微坑会相互叠加,导致坑边消失,微坑也就不能称之为 "坑"。因此,初始需要设置足够大的中心距,并获得不同功率下的微坑直径,再根据微坑直径大小,设置稍大一点的中心距,以获得排列紧密且无叠加的微坑。
图3中单个微坑的直径在28μm左右,坑深度在7.2μm左右,微坑内部结构也比较复杂。
图4为图3蓝色框继续放大5倍的SEM图。可以看出,微坑内部不是平滑的,而是存在分层、突出、蜂窝等各种结构。这样复杂的内部结构更有利于金属层和基材结合。通过调节激光光斑内能量分布,即可调节微坑内部结构。
设置好路径距离和扫描镀速等,可在基材上表面形成无边界叠加的密集排列的微坑(图5)。从切面可观察到,在微坑的中心位置处有等间距的一个个v形小坑(图6)。图7为微坑光学显微镜测试图,该微坑的直径为18μm左右、相邻微坑中心距为20μm。
图5 微坑正面 图6 微坑切面 图7 光学显微镜测试深度
Lpum工艺支持使用紫外皮秒等光斑极小的激光器,激光加工线路可以按照单排成线的方法,加工出和光斑大小接近的极细线路。但是,在后续实际生产中,单排线化学镀时容易断路、增厚镀层过程中镀层向线两边扩散导致线变粗等因素,这种极细线路只有在比较苛刻的条件下才能够实现。下图是在实验室里做出的17μm左右的线路(图8、图9为放大100倍下的图像、图10为放大1000倍下的图像):
图8 样品1(一) 图9 样品1(二) 图10 样品1(三)
虽然20μm以下的极细线路生产难度大,但Lpum工艺能轻易实现生产50~100μm的线路,下图是放大500倍左右的线路图(图11、图12、图13中金属线路宽度在60~70μm左右):
图11 样品2(一) 图12 样品2(二) 图13 样品3
2、镀层与基材的结合力:
现有的大多数类似的工艺,均使用红外连续激光加工烧蚀出蜂窝状的表层以便于活化剂吸附,激光与基材表面反应是升华或汽化和重熔同时作用。单位面积能量(能量密度)需要保持在一定范围,能量密度小,反应以重熔为主,蜂窝孔洞少;能量密度大,以升华或汽化为主,蜂窝层太薄。而且蜂窝层最上层的碳化结构比较松散,如图14、图15中红色圆圈所示。松散结构层会降低结合力。并且,在保持能量密度不变的情况下,增加加工次数时,松散层厚度也随之增加,结合力亦无法提高。
图14 使用红外连续激光的工艺样品切面图 图15 图14蓝色框放大5倍图
相比现有工艺而言,德中Lpum工艺可有效调节微坑的直径和结合力。激光能量密度越大,坑的深度越大,结合力越好。
实验使用三种基材,裁切成10cm*10cm小板,表面全部经Lpum工艺激光加工,后经金属化和镀铜处理,结合力测试如下表所示。测试标准:DIN 51 221, part 1,剥离力测试实验,方法原理如图16所示:
测试结果如下三表:
图16 剥离力实验原理图
激光功率百分比 |
17% |
27% |
51% |
100% |
微坑直径/μm |
10.3 |
12.9 |
14.9 |
26.7 |
微坑深度/μm |
0.5 |
1.06 |
1.77 |
7.9 |
微坑径深比 |
20.6 |
12.1 |
8.4 |
3.4 |
剥离力(kgf/cm) |
0.89 |
1.13 |
1.29 |
1.46 |
表2 FR4基材剥离力测试结果
激光功率百分比 |
17% |
27% |
51% |
100% |
微坑直径/μm |
22.5 |
25.8 |
33.2 |
38.5 |
微坑深度/μm |
2.57 |
2.97 |
2.98 |
5.7 |
微坑径深比 |
8.7 |
8.7 |
11 |
6.7 |
剥离力(kgf/cm) |
0.54 |
0.57 |
0.59 |
0.66 |
表3 LCP基材剥离力测试结果
激光功率百分比 |
10% |
17% |
51% |
100% |
微坑直径/μm |
11.9 |
12.8 |
27.9 |
36.1 |
微坑深度/μm |
1.42 |
1.88 |
8.7 |
18 |
微坑径深比 |
8.4 |
6.8 |
3.2 |
2 |
剥离力(kgf/cm) |
0.62 |
0.83 |
0.98 |
1.32 |
表4 纯环氧树脂基材剥离力测试结果
从上三种材料的规律能看出,能量密度越大,结合力越大。
下图是在63*88mm的ABS板材上,运用Lpum工艺做出的一个微波图形金属导线样品。
图17 ABS基材 图18 激光加工后 图19 金属化后 图20 样品细节
以上结果表明,Lpum工艺作为一种新3D-MID工艺,能在普通材料上实现选择性金属化,加工线路精细,可有效控制基材与线路的结合力。
四、疑问解答
1、该技术适用于所有的塑料吗?
Lpum工艺现阶段能应用于ABS和含ABS的合金(比如ABS+PC)。在高性能塑料中比如PEEK、PPS、LCP上也有突破性进展,后续需进一步细化,目前在研发中。
2、能够使用红外等波长的激光器吗?
只要激光器激发的激光光束能与塑料表面发生反应,Lpum工艺就可适用,但最好是脉冲激光器,因为连续激光加工单独坑洞的效率慢且坑洞直径大。
3、坑深度越大,结合力就越大,那么不断增加加工次数,结合力就会无限大,对吗?
理论上是如此,但在实际生产中,会存在以下三种问题:(1)、增加加工次数会降低加工效率,因此,实际生产中加工次数不能过多;(2)随着坑洞深度增加,增加加工次数,会显著降低加工效果,坑洞深度变化也越来越小;(3)对于厚度比较薄的材料,不允许坑洞深度过大。
4、该技术能达到的最小线宽间距是多少?
最小线宽间距与使用的激光机的光斑直径(聚焦后的光束束腰直径)大小有关。
以开发ABS基材时为例,Lpum工艺可使用红外纳秒、紫外纳秒、紫外皮秒等不同激光机。其中的理论光斑最小的是紫外皮秒,机器的光斑大小为13.95μm,与ABS基材反应后的微坑直径(包括周边热影响区)为15~36μm,单排成线虽能镭射出17μm左右的线,但需要非常精密的设备和精细的管控才能保持好的良率。双排成线相对简单,加上考虑镀层增厚(6-8μm)时侧向扩展,最终可做出50μm左右的线路。那么最小的线宽间距约为50/80μm。
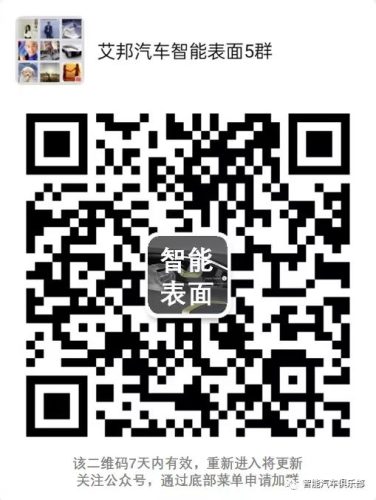